Coaching Leadership in Sustaining a Lean Culture Transformation
DATE & HOST
September 11th 2018
Monterrey, Nuevo Leon.
DESCRIPTION
Most companies embarking on a lean journey soon become frustrated with kaizen events and isolated improvement projects that yield great short-term results but have no sustainability. They are searching for something more: the culture of continuous improvement with its philosophy, processes, and people aligned to cultivate problem solving. In this program we address the top barriers to your lean transformation and what to do about them. These barriers include:
- Overemphasis of “lean tools” and not developing and engaging the people
- Lean being isolated to operations and not connecting functions across the organization
- Taking strategic, aligned, and clear action steps throughout the organization
OBJECTIVES
- Learn actions to immediately improve your profits and cash flow and get the business results your leaders are requiring
- Establish systems to get your people the development and growth they are looking for
- Understand and implement processes and systems to sustain your improvement activity
- Understand how to attract, select, develop and engage competent, able and committed team members and leaders.
AIMED AT
Executive Leaders, General Managers, Supervisors, Lean Leaders, and any one facilitating change within your organization who understand the importance of going beyond tools to creating effective management systems and processes in order to set the basis for creating a sustainable lean, problem solving culture across the entire organization.
PROGRAM
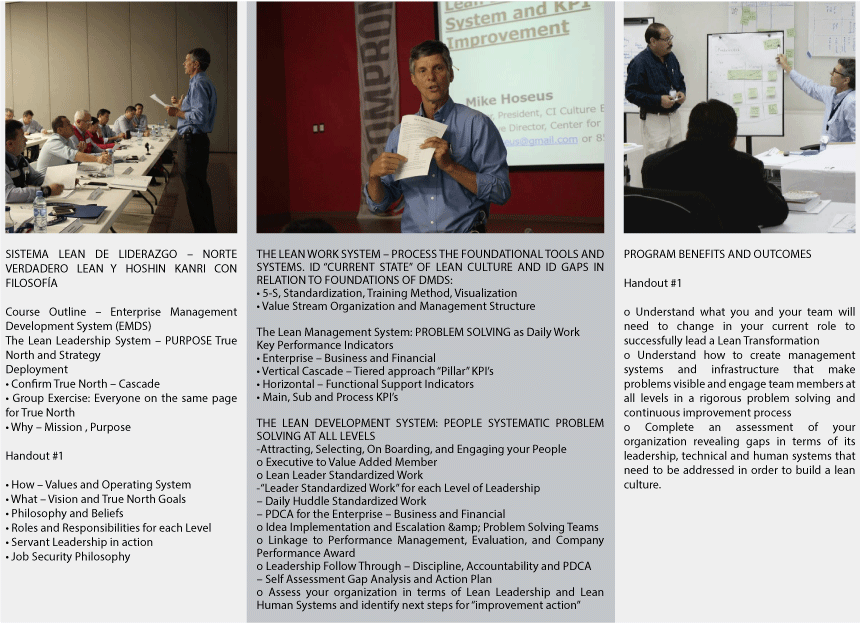
Gallery of previous courses
INSTRUCTOR
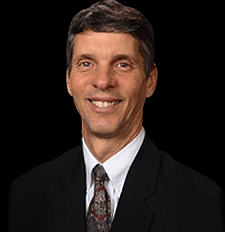
MICHAEL HOSEUS
ALFRA Toyota Team Director Former Executive Plant Manager of Toyota Kentucky
- Best Seller of the Toyota Culture
- Associate Executive Advisor for ALFRA Lean Advisors
- Former Toyota Assistant General Manager
- Former Assistant General Manager and Human Resources
- Executive Director CQPO
Mike is Executive Director for the Center for Quality People & Organizations (CQPO). Mike Hoseus brings both manufacturing operations and specialization in Human Resource experience to CQPO. CQPO is an organization developed in 1999 as a vision of Toyota Motor Manufacturing to share Lean Quality philosophy and human resource practices with education, business, and community organizations. CQPO current projects with Toyota include New Hire selection and training process, Team Leader and Group Leader post promotion training, Quality Circle Leader and Manager training, and Global Problem Solving for all levels. Mike is an adjunct professor with the University of Kentucky’s Lean Manufacturing Program. Mike is co author with Dr. Jeffery Liker (Author of the Toyota Way) of Toyota Culture. Mike is an adjunct professor with the University of Kentucky’s Center for Manufacturing and a member of the faculty of Lean Enterprise Institute. Mike is also president of Lean Culture Enterprises. Prior to CQPO, Mike was a corporate leader for 13 years at Toyota Motor Manufacturing’s Georgetown, Kentucky, plant both in Human Resources and Manufacturing. As Assistant General Manager in Human Resources, his responsibilities included personnel, safety, HR development, employee relations, benefits, training, and manufacturing/human resource teams for a plant of 8000 team members. His major initiative was development of the enhanced relationship between Human Resource and Manufacturing Mike’s operational responsibilities in manufacturing started in 1987 as a front line supervisor in vehicle assembly. This included all aspects of safety, quality, productivity, cost and morale for operations. With experience as Assembly Plant Manager and eventually Assistant General Manager, his responsibilities increased to include both assembly plants including operations, maintenance, and engineering. He is a Certified Trainer in Global Problem Solving & Waste Reduction, Standardized Work and Kaizen Events.
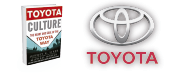
SERVICIOS INCLUIDOS
- Manual in Color.
- Coffee Break and lunch.
- Course Certificate
- Exclusive for 25 participants.
So we can know more about your needs
So we can know more about your needs