LEAN SYSTEMS FOR LEADERSHIP ACCOUNTABILITIES
LEAN SYSTEMS FOR LEADERSHIP ACCOUNTABILITIES
DATE & HOST
DATE & HOST
To be defined
Improvement system for operations and scope of objectives through Management Coaching and Media Management.
DESCRIPTION:
The Leader: key piece in the results and sustainability of an organization. The most common challenges presented by the leaders are precisely in the main roles that need to be carried out every year and every day: dynamic alignment of the entire organization, effective management of the different areas of the business at all levels and the continuous development of both the processes as of the personnel, everything, to achieve the short-term objectives and the long-term sustainability.
The Lean Systems that every Leader in Toyota applies as a support and guide in their own way to success in their main roles are:
- Hoshin Kanri – Dynamic Strategic Planning.
- EMDS: Enterprise Management Development System. For the daily / weekly / monthly / annual effectiveness of the entire organization.
- Toyota Kata. Expand knowledge and organizational learning processes to better results.
Entrenamiento Toyota Kata Infield WESTROCK BrasilEntrenamiento Toyota Kata Infield WESTROCK Brasil
Posted by ALFRA Lean Advisors on Wednesday, March 29, 2017
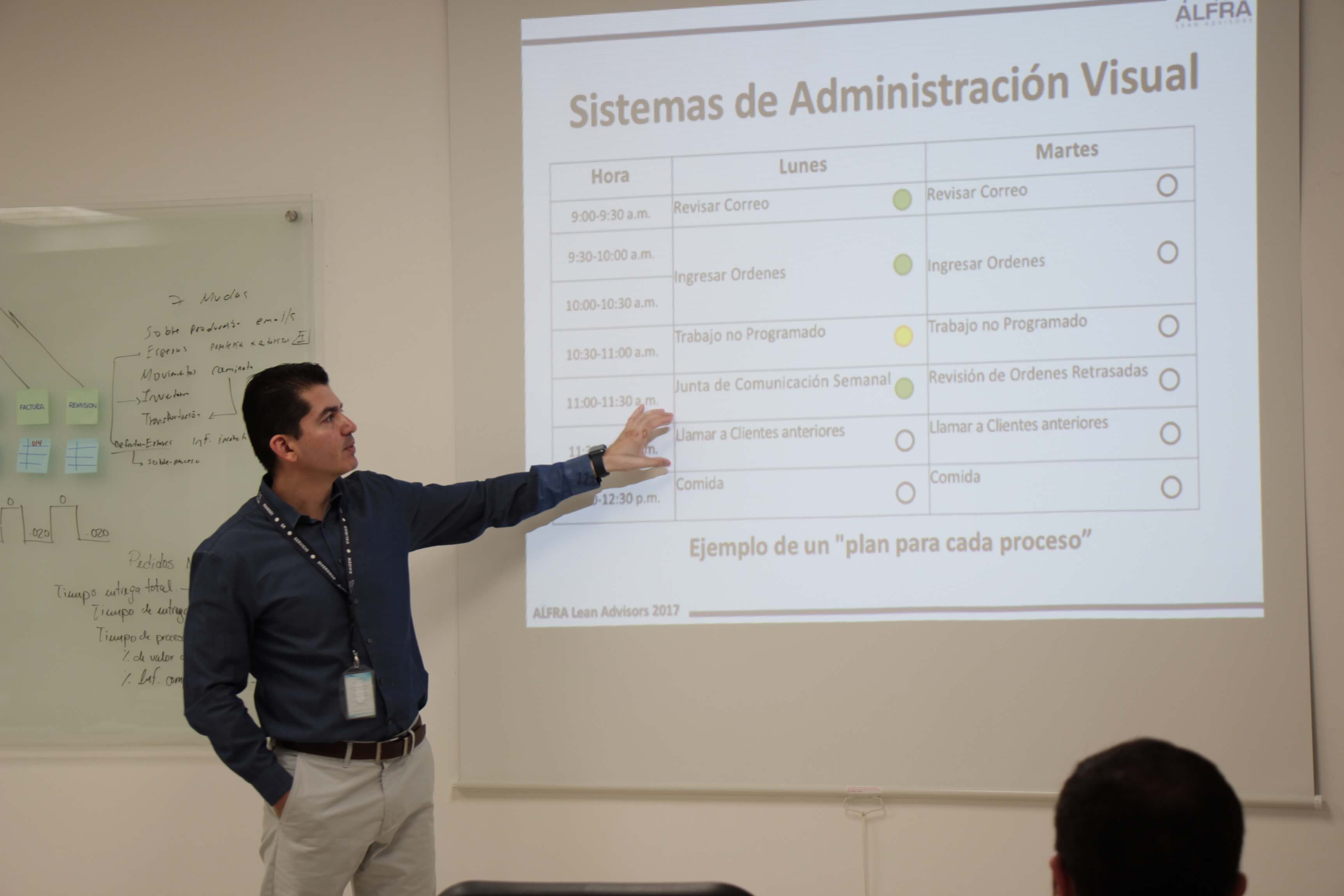
OBJECTIVES
Understand the characteristics of Lean Systems for Leadership and how they interrelate to facilitate the inter-connected work of all Leaders of any organization.
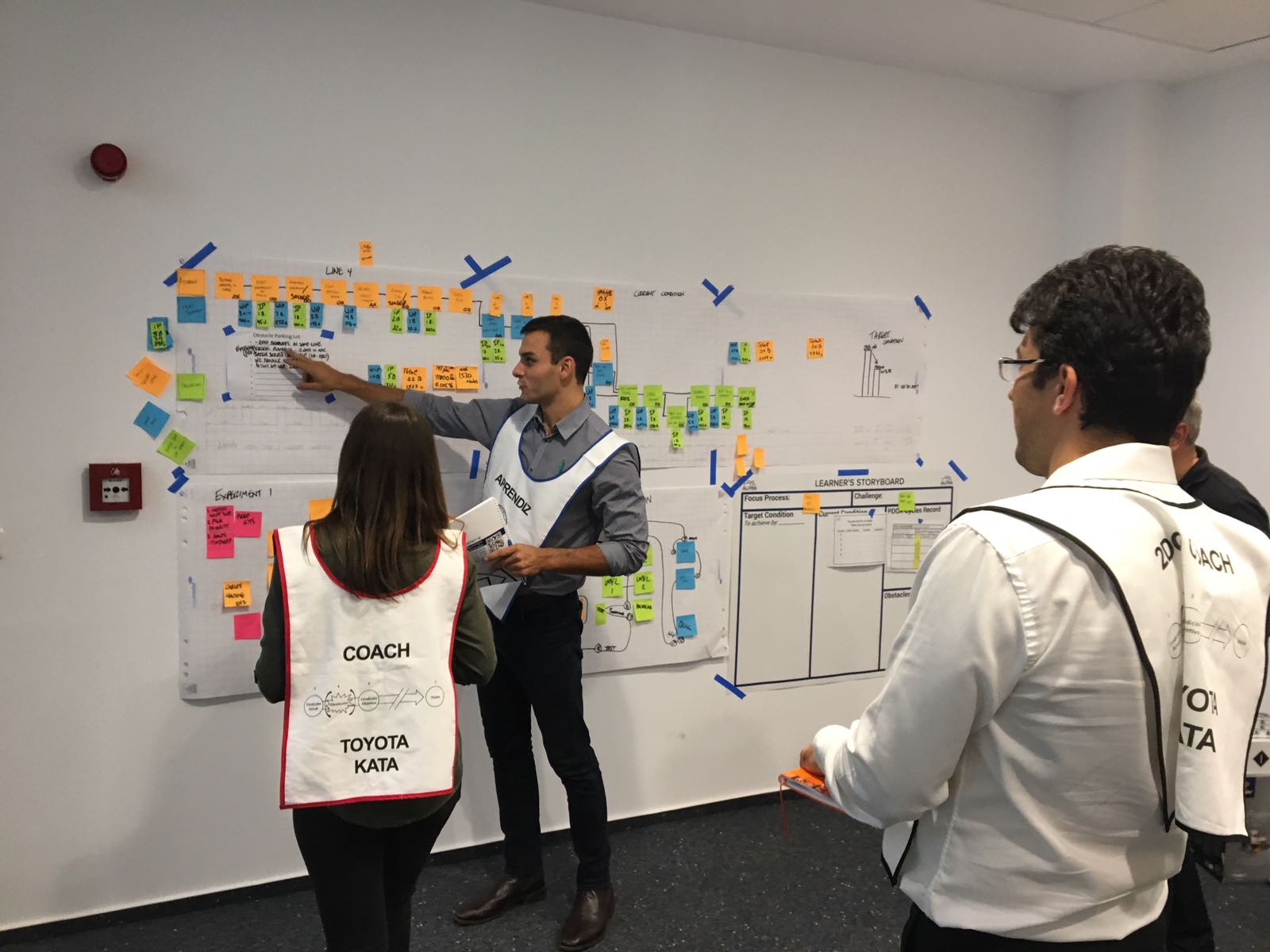
OBJECTIVES
Understand, under a theoretical and practical method, each of the Lean systems and how they can be applied to each organization.
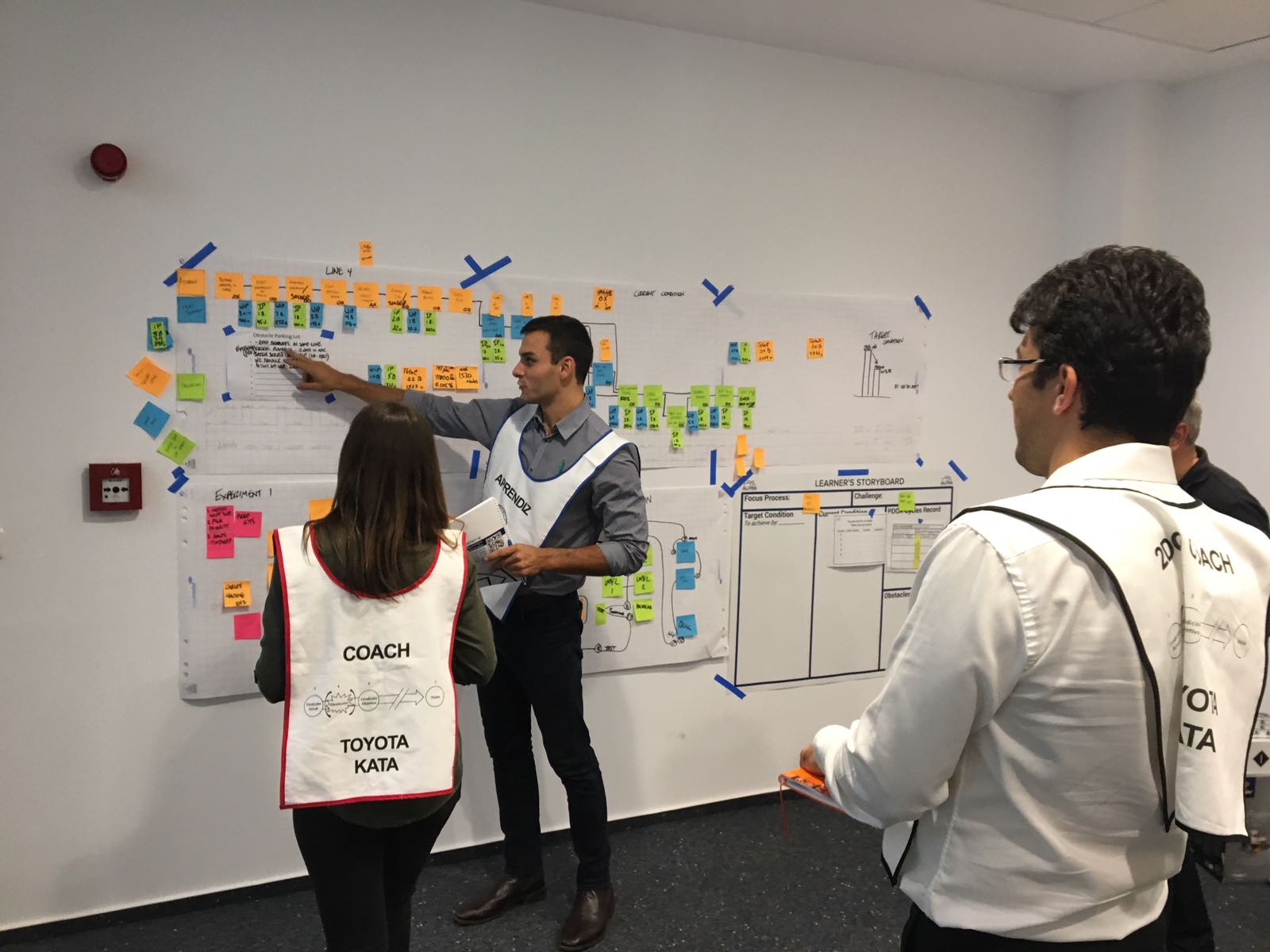
OBJECTIVES
Know the Lean Systems for Leadership applied in a Company and share the challenges and benefits that come with its implementation and daily operation.
AIMED AT:
CEO, President, Vice Presidents, Executive Leaders, General Managers, Lean Leaders, and anyone who facilitates change within their organization who understand the importance of going beyond the tools for creating effective management systems and processes in order to to lay the foundations for the creation of a sustainable lean culture.
OBJECTIVES
- Understand the characteristics of Lean Systems for Leadership and how they interrelate to facilitate the inter-connected work of all Leaders of any organization.
- Understand, under a theoretical and practical method, each of the Lean systems and how they can be applied to each organization.
- Know the Lean Systems for Leadership applied in a Company and share the challenges and benefits that come with its implementation and daily operation.
AIMED AT:
CEO, President, Vice Presidents, Executive Leaders, General Managers, Lean Leaders, and anyone who facilitates change within their organization who understand the importance of going beyond the tools for creating effective management systems and processes in order to to lay the foundations for the creation of a sustainable lean culture.
PROGRAM
26th & 27th: HOSHIN KANRI |
---|
![]() |
Improvement SeminarI. WELCOME & PLANT TOUR II. Hoshin Kanri – Dynamic strategic planning. Introduction.
Lean Leadership System: process of implementing strategies in 6 steps. Evaluation – Determine “Current status – Future state and gaps to be addressed”
Development system (EMDS)
Exercise: create the strategic plan: prioritize and select “key elements of lean”
III. EMDS: Business management development system. For the daily / weekly / monthly / annual effectiveness of the entire organization. |
27th & 28th: EMDS
|
![]() |
General Elements of EMDS
Operation Management Boards
Standardized Work of Leaders
Accountability Meetings (Tier Meetings)
Discipline
IV. Toyota Kata. Expand knowledge and organizational learning processes to better results.
|
29th & 30th: TOYOTA KATA
|
![]() |
FOCUS ON EDUCATION
FOCUS ON CHALLENGES
|
26th & 27th: HOSHIN KANRI | 27th & 28th: EMDS | 29th & 30th: TOYOTA KATA |
![]() |
![]() |
![]() |
Improvement SeminarI. WELCOME AND PLANT TOUR II. Hoshin Kanri – Dynamic strategic planning. Introduction.
Lean Leadership System: process of implementing strategies in 6 steps. Evaluation – Determine “Current status – Future state and gaps to be addressed”
Connection to the Lean Management system and Enterprise Management Development System (EMDS)
Exercise: create the strategic plan: prioritize and select “key elements of lean”
III. EMDS: Business management development system. For the daily / weekly / monthly / annual effectiveness of the entire organization. |
General Elements of EMDS
Operation Management Boards
Standardized Work of Leaders
Accountability Meetings (Tier Meetings)
Discipline
IV. Toyota Kata. Expand knowledge and organizational learning processes to better results.
|
Focus on Education
Focus on Challenges
|
INSTRUCTORS
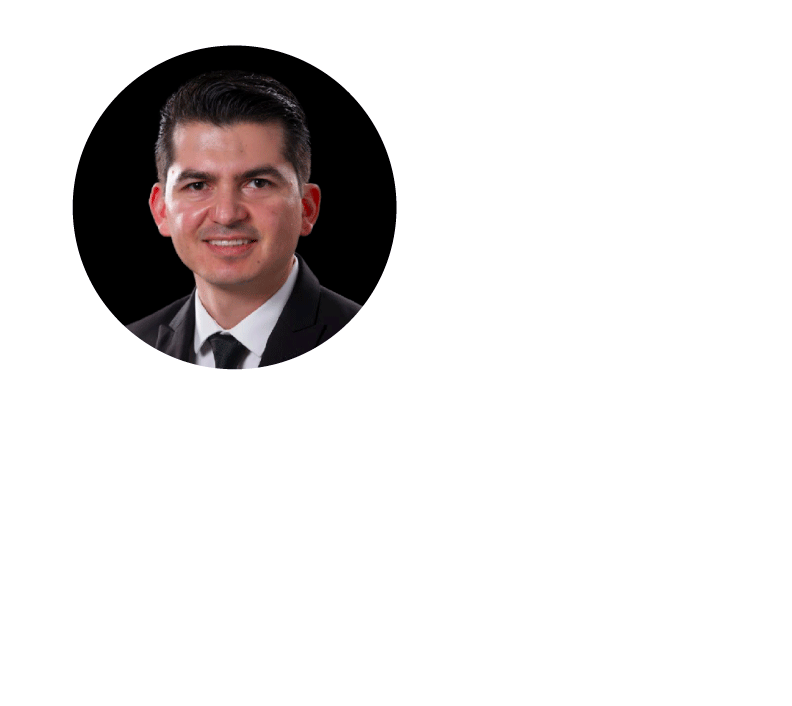
Francisco Ocejo is leading Alfra Lean Advisors a Consulting firm with over 1,500 customers companies from 14 countries around the world. ALFRA Support companies Lean transformation from Strategic Planning, SCM, OPS, HR, Sales, Finance.
He has been learning, applying, and teaching the Toyota Production System in Canada, USA, Mexico, Latin America & Europe. He has taught and applied Lean from the senior management level to the operational levels closest to Gemba fro over 150 companies from international corporations, to mid-size and small family businesses from diferent industry sectors such as: Service, Logistics, Aerospace, Automotive, Electronic, Bank, Ceramic, Education, Defense Electronic, Food & Beverage, Gas & Oil, Electric Manufacturing, and several manufacturing sectors.
Francisco is a Toyota Kata Ambassador and Pioneer to spread the Toyota Kata in Mexico, he has been applying TK with his colleague Dr. Jeff Liker ( author of the best seller the toyota Way) and many other Coaches in companies with the hieghest TPS people development.
For over 5 years he has been constantly trained by the Best Seller “Toyota Way (800 hrs),” the Ex President of JV Toyota China Mr Shingo (360 hrs), and various Toyota top Management ( + 1000 hrs).
His best expertise is in: Coaching Toyota Kata, Lean Manufacturing ,Lean Office, Lean Culture and Business Transformation.
He is an Industrial and Systems Engineering at the Monterrey Technical Institute. He has taught classes for students in over 15 Universities, lecturing in various Congresses in Mexico. Certified as Black Belt Six Sigma at Institution of Industrial Engineers, and the Theory of Constraints and Thinking Process at the EGADE of the Monterrey Technical Institute.
Francisco is a former Celestica leader & manager of the Lean Culture Transformation, with BlackBerry (RIM), Palm, HTC as Principals customers, with sales of over 1 billion dollars. This transformation involved over 5,000 people.


Based on his broad experience, Gustavo is expert applying a suitable approach for Continuous Improvement needed on the different organizations from a Business results optic, becoming an effective Coach for Top Management and support for The Toyota Way roles. Gustavo has learned The Toyota Way directly from its Author, Dr. Jeff Liker, and has applied it on Gemba as a Team with many Executives from Toyota specialized on General Management, TPM, Lean Mfg Tools, and Supply Chain. Gustavo has taught the Toyota Production System at all organizational levels and has applied over 50 companies of different sizes: Lean Leadership Systems (Hoshin Kanri, FMDS, and 8-Step Problem Solving), Toyota Kata for development, Supply Chain Management, TPM, Lean Manufacturing tools (5S’s, SW, SMED, Jidoka, Poka Yoke, Heijunka, JIT, etc.), and Lean Office approach. On Six Sigma, Gustavo as Master Black Belt has trained and certified +500 Black Belts, Green Belts, and Yellow Belts. Gustavo has +20 years of experience on Continuous Improvement, Manufacturing, Process Engineering and Quality in large companies: Motor Wheel (Automotive), Kodak, Philips, Daltile, American Standard. He has +12 years of experience as Vice/President Staff as Continuous Improvement Director for American Standard México and Master Black Belt Champion for Daltile México. He has deployed programs that have achieved +$110 Million USD in savings with +3,000 projects on all departments: R&D, Engineering, Manufacturing, Maintenance, Quality, Logistics, Supply Chain, Sales, Marketing, Finance, HR, Energy. Over his 22 years experience, Gustavo has been exposed to many different organizations applying suitable Lean approaches on a variety of systems with diversity on leadership styles.
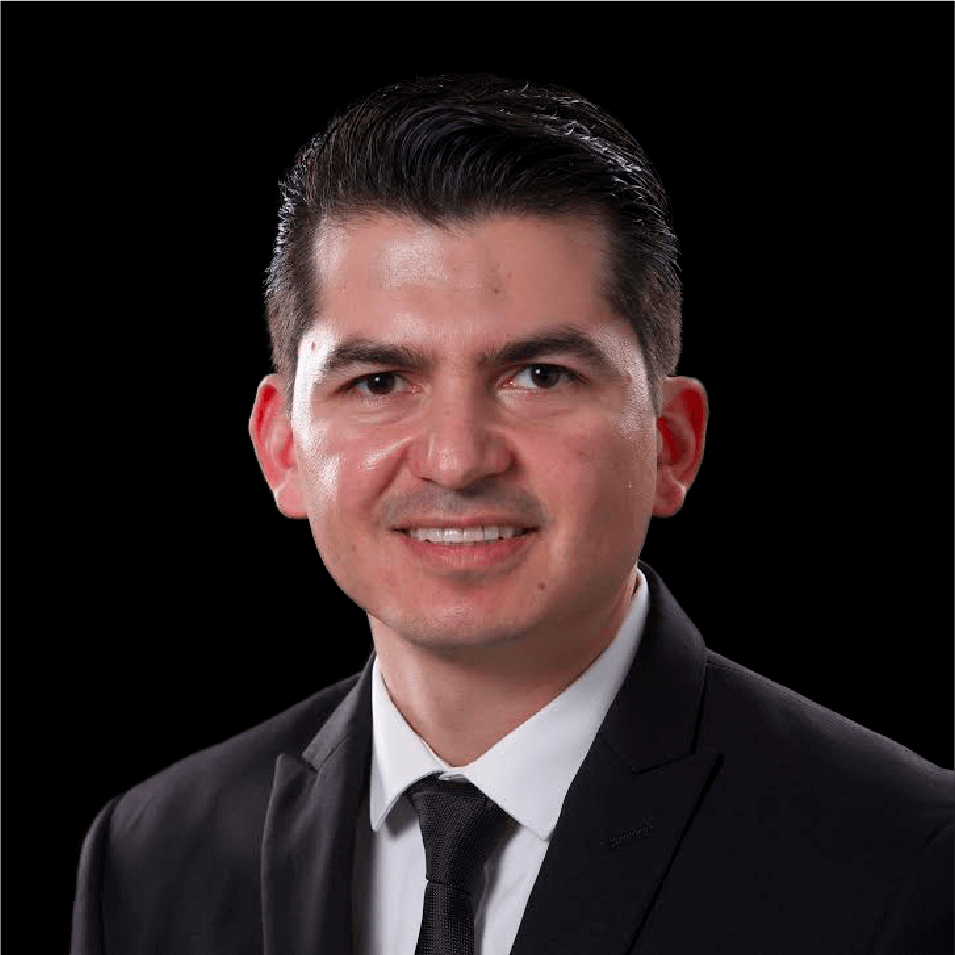
FRANCISCO OCEJO
Liker Lean Advisors Vice President
Toyota Kata Ambassador
Former VP IISE
Former Lean Manager at Celestica
Education
B.S. Industrial Engineering at Tec de Monterrey
Several Lean Certifications for international Institutes
Francisco Ocejo is leading Alfra Lean Advisors a Consulting firm with over 1,500 customers companies from 14 countries around the world. ALFRA Support companies Lean transformation from Strategic Planning, SCM, OPS, HR, Sales, Finance.
He has been learning, applying, and teaching the Toyota Production System in Canada, USA, Mexico, Latin America & Europe. He has taught and applied Lean from the senior management level to the operational levels closest to Gemba fro over 150 companies from international corporations, to mid-size and small family businesses from diferent industry sectors such as: Service, Logistics, Aerospace, Automotive, Electronic, Bank, Ceramic, Education, Defense Electronic, Food & Beverage, Gas & Oil, Electric Manufacturing, and several manufacturing sectors.
Francisco is a Toyota Kata Ambassador and Pioneer to spread the Toyota Kata in Mexico, he has been applying TK with his colleague Dr. Jeff Liker ( author of the best seller the toyota Way) and many other Coaches in companies with the hieghest TPS people development.
For over 5 years he has been constantly trained by the Best Seller “Toyota Way (800 hrs),” the Ex President of JV Toyota China Mr Shingo (360 hrs), and various Toyota top Management ( + 1000 hrs).
His best expertise is in: Coaching Toyota Kata, Lean Manufacturing ,Lean Office, Lean Culture and Business Transformation.
He is an Industrial and Systems Engineering at the Monterrey Technical Institute. He has taught classes for students in over 15 Universities, lecturing in various Congresses in Mexico. Certified as Black Belt Six Sigma at Institution of Industrial Engineers, and the Theory of Constraints and Thinking Process at the EGADE of the Monterrey Technical Institute.
Francisco is a former Celestica leader & manager of the Lean Culture Transformation, with BlackBerry (RIM), Palm, HTC as Principals customers, with sales of over 1 billion dollars. This transformation involved over 5,000 people.

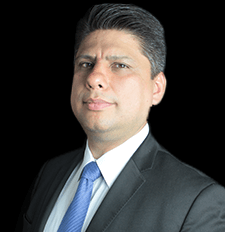
GUSTAVO VARELA
IMA, MBA, MBB. Director División de Consultoría
Based on his broad experience, Gustavo is expert applying a suitable approach for Continuous Improvement needed on the different organizations from a Business results optic, becoming an effective Coach for Top Management and support for The Toyota Way roles. Gustavo has learned The Toyota Way directly from its Author, Dr. Jeff Liker, and has applied it on Gemba as a Team with many Executives from Toyota specialized on General Management, TPM, Lean Mfg Tools, and Supply Chain. Gustavo has taught the Toyota Production System at all organizational levels and has applied over 50 companies of different sizes: Lean Leadership Systems (Hoshin Kanri, FMDS, and 8-Step Problem Solving), Toyota Kata for development, Supply Chain Management, TPM, Lean Manufacturing tools (5S’s, SW, SMED, Jidoka, Poka Yoke, Heijunka, JIT, etc.), and Lean Office approach. On Six Sigma, Gustavo as Master Black Belt has trained and certified +500 Black Belts, Green Belts, and Yellow Belts. Gustavo has +20 years of experience on Continuous Improvement, Manufacturing, Process Engineering and Quality in large companies: Motor Wheel (Automotive), Kodak, Philips, Daltile, American Standard. He has +12 years of experience as Vice/President Staff as Continuous Improvement Director for American Standard México and Master Black Belt Champion for Daltile México. He has deployed programs that have achieved +$110 Million USD in savings with +3,000 projects on all departments: R&D, Engineering, Manufacturing, Maintenance, Quality, Logistics, Supply Chain, Sales, Marketing, Finance, HR, Energy. Over his 22 years experience, Gustavo has been exposed to many different organizations applying suitable Lean approaches on a variety of systems with diversity on leadership styles.
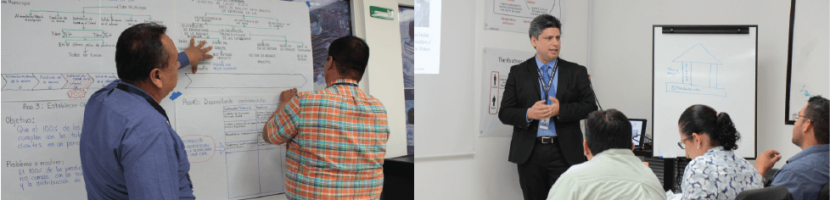
INCLUDED SERVICES
Manual
Coffee break & Lunch
Certification
INCLUDED SERVICES
- Digital Manual
- Coffee Break y comida.
- Certification