PROBLEM SOLVING
DATE & LOCATION
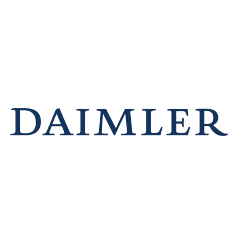
Problem Solving
Problem Solving is the basis of Lean. The tools of a Lean Production System are designed to identify problems. Do you have standardization and experience in all levels of your organization to solve them? The extent to which training and your organization's involvement in problem solving will determine your success in your efforts of Lean. It will be reviewed how a Lean Organization establishes its culture to solve problems for all levels, giving participants the opportunity to practice the 8-Step Method by analyzing real problems in team with a coaching through the whole process.
BY ASSISTING THIS COURSE YOU WILL ACHIEVE:
Develop critical thinking to help the individual truly solve problems from the root to restore systems of Quality, Maintenance, Supply Chain, Security, Human Resources, Production and many other aspects that have an unknown cause.
COMPANIES | LOGO | PROGRAM |
---|---|---|
San Mina- GDL | ![]() |
Lean Office |
Hammond Power Solutions | ![]() |
Problem Solving |
Rockwell (Canada & Monterrey) | ![]() |
TPS Gemba Training |
Nemak | ![]() |
EMDS |
CEMEX | ![]() |
TPM Mtto. Total Toyota Productive |
Kimball Electronics | ![]() |
TPS Gemba Training |
Frisa | ![]() |
Lean Office |
SKF | ![]() |
Planification and control of the production
TPS Gemba Training |
Sogefi Group | ![]() |
TPM Mtto.Total Toyota Productive |
Silgan- San Luis | ![]() |
Planification and control of the production
TPM Mtto. Total Toyota Productive TPS Gemba Training |
Avanzar Interior Technologies | ![]() |
Toyota Kata in Field |
Daimler Mercedes Benz | ![]() |
TPS Gemba Training
Toyota Kata in Field |
OBJECTIVES
1. Work as a team in solving “real-time” problems on the production floor with real problems identified by the organization.
2. Learn from the treasury of Toyota Tools: “Go to See”, “Separating a Problem” and “Root Cause Analysis 5-Why”
3. Guidance and coaching by the Instructor through the problem solving process.
4. Learn how to complete, present, and give feedback on the Troubleshooting A-3.
AIMED AT
Director, Managers and Middle Managers from all areas of the organization.
The program is divided into 3 parts:
- Pre-Work. Two days prior to the session, with the assistance of the organization, we will select the actual problems to be attacked during the course.
- The day of the session begins by covering the general concepts of Lean and presents the 8-Step Problem Solving method by reinforcing them with case studies.
- The second part consists of team activity, applying the 8 Steps in the Problems previously selected, with the Coaching of the instructor.
SOLVING PROBLEMS SYSTEMATICALLY APPLYING THE TOYOTA METHOD
- Make your organization capable of identifying and responding to problems “as they occur”.
- Understand how a problem-solving system is a dynamic process that continually improves itself and the people involved. Learn how to implement it in your organization.
- Evaluate the current state of your organization in establishing, implementing and sustaining daily problem solving.
- Learn the role that all levels play in problem solvings.
- Learn the basic A3 formats and their uses in the management process.
PROGRAM
Day 1 | Day 2 |
---|---|
![]() |
![]() |
INTRODUCTION
LEARNING THE BASIC FORMATS OF A3 AND ITS USES IN THE MANAGEMENT PROGRAM
8 PROBLEM SOLVING STEPS
|
8 STEP PRACTICE FOR PROBLEM SOLVING
8 PROBLEM SOLVING STEPS (CONT.)
APPLICATION OF THE 8 STEPS IN REAL PROBLEM SOLVING – OFFERING THE
|
INSTRUCTOR
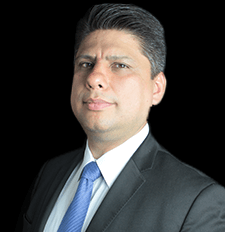
GUSTAVO VARELA
IMA, MBA, MBB. Director División de Consultoría
Based on his broad experience, Gustavo is expert applying a suitable approach for Continuous Improvement needed on the different organizations from a Business results optic, becoming an effective Coach for Top Management and support for The Toyota Way roles. Gustavo has learned The Toyota Way directly from its Author, Dr. Jeff Liker, and has applied it on Gemba as a Team with many Executives from Toyota specialized on General Management, TPM, Lean Mfg Tools, and Supply Chain. Gustavo has taught the Toyota Production System at all organizational levels and has applied over 50 companies of different sizes: Lean Leadership Systems (Hoshin Kanri, FMDS, and 8-Step Problem Solving), Toyota Kata for development, Supply Chain Management, TPM, Lean Manufacturing tools (5S’s, SW, SMED, Jidoka, Poka Yoke, Heijunka, JIT, etc.), and Lean Office approach. On Six Sigma, Gustavo as Master Black Belt has trained and certified +500 Black Belts, Green Belts, and Yellow Belts. Gustavo has +20 years of experience on Continuous Improvement, Manufacturing, Process Engineering and Quality in large companies: Motor Wheel (Automotive), Kodak, Philips, Daltile, American Standard. He has +12 years of experience as Vice/President Staff as Continuous Improvement Director for American Standard México and Master Black Belt Champion for Daltile México. He has deployed programs that have achieved +$110 Million USD in savings with +3,000 projects on all departments: R&D, Engineering, Manufacturing, Maintenance, Quality, Logistics, Supply Chain, Sales, Marketing, Finance, HR, Energy. Over his 22 years experience, Gustavo has been exposed to many different organizations applying suitable Lean approaches on a variety of systems with diversity on leadership styles.
SERVICES INCLUDED
The Training Certificate will be issued 6 months after attending the course, presenting the implementation and results obtained.
- Manual
- Training Diploma
- Coffee Break
- Lunch
- Implementation Formats and Templates for Lean Systems and Tools