Business Case: OEE Improvement By Applying TPM & Toyota Kata
DATE & HOST
OEE Improvement By Applying TPM & Toyota Kata
August 27th-31th 2018
Grandview Misuri, USA.
Benefits Improving OEE with TPM & Toyota Kata
OBJECTIVES
-
To get an overview on how to implement TPM in your company
- How TPM improves the teamwork of maintenance, production, engineering, and management
- Learn why TPM is at the base of TPS and how TPM will give your company a strong foundation for manufacturing excellence
- Implement the first, basic TPM elements as a foundation for the complete TPM System.
- Understand the Toyota Kata approach as the 4th Pillar of TPM
- Develop Lean Coaching Skills within the Maintenance and Production Team in order to Improve the Equipment. Always.
AIMED AT:
- Plant Managers
- Maintenance – Manufacturing – Engineering Managers/Supervisors, Key Maintenance/Production Team Members, and Lean leaders that would like to understand the correct implementation of TPM
AGENDA
Día 1 | Día 2 | Día 3 | Día 4 | Día 5 |
---|---|---|---|---|
![]() |
![]() |
![]() |
![]() |
![]() |
DAY 1 – AMMODULE 1. Toyota’s Equipment Maintenance Theory The 4 Pillars of TPM activity. Toyota Total Productive Maintenance (TPM) Toyota’s DAY 1 – PMMODULE 2. Failure Occurence Prevention Toyota Total Productive Maintenance Visual Elements to Facilitate Operation and |
DAY 2 – AM5 Senses on the Shop Floor (cont) Autonomous Maintenance: Steps for Implementing Operator’s Maintenance on Shop DAY 2 – PMAutonomous Maintenance: Steps for Implementing Operator’s Maintenance on Shop Breakdown Analysis Visual Preventive Maintenance on Shop Floor |
DAY 3 – AMVisual Preventive Maintenance (cont) Predictive Maintenance Board Management MODULE 3. Foundation Systems: HR Development for Maintenance and HR on Maintenance Fundamental Concepts: 4 major items for TL Role DAY 3 – PMMODULE 4. Hoshin Alignment: Management System applied to Maintenance Toyota FMDS for Maintenance Management. MODULE 5. Implementing TPM Strategy to Implement TPM on Plant |
DAY 4 – AMMODULE 6 Improvement Kata: The Challenge Project Introduction Group Work: First team meeting Improvement Kata: Current State Analysis DAY 4 – PMGroup Work: Current State Analysis Group Present Current State Analysis & Conclusions |
DAY 5 – AMMODULE 7 Improvement Kata: First Target Condition Group work: Define 1st target condition and identify obstacles on storyboard Improvement Kata: PDCA cycles Go to Enterprise to run 1st experiment Fill storyboard- 1st experiment Coaching Kata Overview DAY 5 – PMCoaching cycle in front of the group ALFRA Instructors Coaching cycle with your team Go to Enterprise to run 2nd experiment Fill storyboard-2nd experiment Coaching cycle in front of the class & Conclusion Final presentation to Silgan Top management Learning reflections and next steps |
INSTRUCTORS
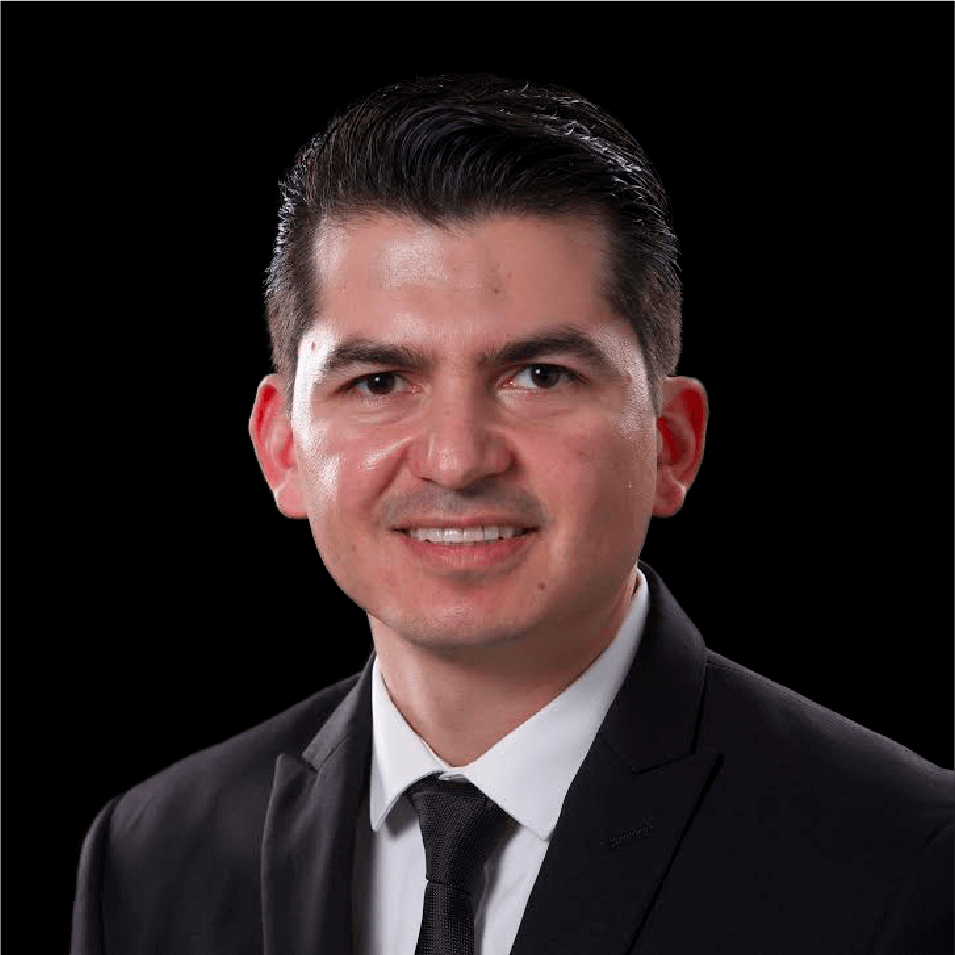
FRANCISCO OCEJO
Director general ALFRA Embajador Toyota Kata México Experiencia Toyota Kata Europa, Norte América y Sudamérica.
Francisco Ocejo is leading Alfra Lean Advisors a Consulting firm with over 1,500 customers companies from many countries. He also is the Vice President of Alfra Institute, a education organization to develop the top Management under a Lean MBA degree formed with Former Toyota executives and Top worldwide Management.
He has been learning, applying, and teaching the Toyota Production System in Canada, USA, Mexico, Latin America & Europe. He has taught and applied Lean Manufacturing tools (5S’s, SW, SMED, Jidoka, Poka Yoke, Heijunka, JIT, etc.), from the senior management level to the operational levels closest to Gemba fro over 150 companies from international corporations, to mid-size and small family businesses from diferent industry sectors such as: Service, Logistics, Aerospace, Automotive, Electronic, Bank, Ceramic, Education, Defense Electronic, Food & Beverage, Gas & Oil, Electric Manufacturing, and several manufacturing sectors.
Francisco is a Toyota Kata Ambassador and Pioneer to spread the Toyota Kata in Mexico, he has been applyingTK with his colleague Dr. Jeff Liker ( author of the best seller the toyota Way) and many other Coaches in companies with the hieghest TPS people development.
For over 5 years he has been constantly trained by the Best Seller “Toyota Way (800 hrs),” the Ex President of JV Toyota China Mr Shingo (360 hrs), and various Toyota top Management ( + 1000 hrs).
His best expertise is in: Coaching Toyota Kata, Lean Manufacturing ,Lean Office, Lean Culture and Business Transformation.
He is an Industrial and Systems Engineering at the Monterrey Technical Institute. He has taught classes for students in over 15 Universities, lecturing in various Congresses in Mexico. Certified as Black Belt Six Sigma at Institution of Industrial Engineers, and the Theory of Constraints and Thinking Process at the EGADE of the Monterrey Technical Institute.
Francisco is a former Celestica leader & manager of the Lean Culture Transformation, with BlackBerry (RIM), Palm, HTC as Principals customers, with sales of over 1 billion dollars. Thistransformation involved over 5,000 people.

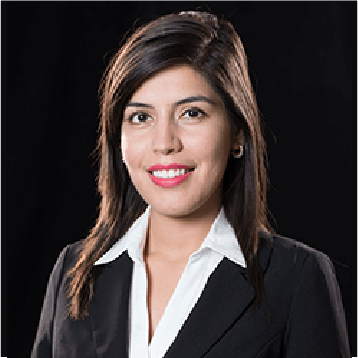
LIDIA FLORES
Consultor Lean en ALFRA / Ha entrenado a más de 100 clientes en Lean Office, Lean Manufacturing y Toyota Kata, incluyendo Gerentes Generales.
Lidia has experience on the Toyota Way, Toyota Kata, Lean Leadership, Gemba Training for the last 2 years, she had been trained by Francisco Ocejo, Alfra Consulting Director Manager; Jeffrey Liker, author of the international best-seller The Toyota Way: 14 Management Principles; Ritshuo Shingo, who is Shigeo Shingo son and was the first president of JV Toyota China in 1998; Gary Convis, who was the first not Japanese President of JV Toyota in Kentucky, and other Top Management. Lidia has trained more than 100 clients on Lean Manufacturing, including General Managers, Manufacturing engineer, Quality, Finance and Logistics. She also is Lean Office Instructor with experience on Logistics, Service company, Human Resources, Purchasing and Engineering change projects improvement. Lidia´s principal customers and trainings: – Daimler Mercedes Benz, a bus assembly division; Lean Office and Toyota Kata training where we improve the engineering change applying Lean Office, we also reduce from 8 to 4 operators on the harness operation line in 3 days. – San Mina, an Oil and Gas Company, Lean Office training and consulting, we reduce the total lead time from 10 to 5 days on the logistic chain including planning, purchasing, materials and engineering. – DeAcero, wire division and steel. She participate on the DeAcero Production System, developing a continuous improvement system for logistic, purchasing, planning, shipping and production. She has taught classes on Lean Manufacturing, Lean Logistics, Toyota Kata and Lean Office for different Universities as Tecnológico de Monterrey, UANL, UDEM, Universidad de Poza Rica, Universidad de Anáhuac, UPAEP. Continuously, she is investigating and developing material for Lean Manufacturing, Lean Office and Toyota Kata training.

GUSTAVO VARELA
Former American Standard Continuous Improvement Director
Former Daltile Master Black Belt
22 years experience. +17 years as Global Continuous Improvement Leader
Education
Bachelor of Mechanics and Administration
MBA from UANL
Master Black Belt certified by ITESM.
Based on his broad experience, Gustavo is expert applying a suitable approach for Continuous Improvement needed on the different organizations from a Business results optic, becoming an effective Coach for Top Management and support for The Toyota Way roles. Gustavo has learned The Toyota Way directly from its Author, Dr. Jeff Liker, and has applied it on Gemba as a Team with many Executives from Toyota specialized on General Management, TPM, Lean Mfg Tools, and Supply Chain. Gustavo has taught the Toyota Production System at all organizational levels and has applied over 50 companies of different sizes: Lean Leadership Systems (Hoshin Kanri, FMDS, and 8-Step Problem Solving), Toyota Kata for development, Supply Chain Management, TPM, Lean Manufacturing tools (5S’s, SW, SMED, Jidoka, Poka Yoke, Heijunka, JIT, etc.), and Lean Office approach. On Six Sigma, Gustavo as Master Black Belt has trained and certified +500 Black Belts, Green Belts, and Yellow Belts. Gustavo has +20 years of experience on Continuous Improvement, Manufacturing, Process Engineering and Quality in large companies: Motor Wheel (Automotive), Kodak, Philips, Daltile, American Standard. He has +12 years of experience as Vice/President Staff as Continuous Improvement Director for American Standard México and Master Black Belt Champion for Daltile México. He has deployed programs that have achieved +$110 Million USD in savings with +3,000 projects on all departments: R&D, Engineering, Manufacturing, Maintenance, Quality, Logistics, Supply Chain, Sales, Marketing, Finance, HR, Energy. Over his 22 years experience, Gustavo has been exposed to many different organizations applying suitable Lean approaches on a variety of systems with diversity on leadership styles.
INCLUDED SERVICES
-
Manual to Color.
-
Coffee Break and food.
-
Course certificate