Designing & Building The Lean Enterprise: Daily Management Development System
Date & Location
November 13th to 15th, Monterrey, Nuevo León
Host: Mercedes-Benz DAIMLER

WORKSHOP DESCRIPTION
Most companies embarking on a lean journey soon become frustrated with improvement events and isolated projects that yield great short-term results but have no sustainability and no major innovation.. They are searching for something more: the culture that goes beyond “just managing” continuous improvement. Success in today’s world of constant change and chaos requires leadership to leverage this uncertainty. It does no good to improve your path if you need to actually change the path you’re on.
Celestica offers flexible and innovative solutions to our customers through our Centers of Excellence. Leveraging our network of preferred suppliers, we help you bring your highly complex products to the market quickly, reliably and with a high level of quality.
The Monterrey operation of Celestica provides assembly of printed circuits, system assembly, box construction, value-added engineering, supply chain management, testing, direct compliance and repair, supported by solid laboratories of materials and test development equipment . The site serves customers in the communications and business market segments.
MAIN CELESTICA CUSTOMERS
Mercedes-Benz DAIMLER
Daimler Buses in Mexico, has a manufacturing plant in Monterrey, Nuevo León. After more than 15 years it has positioned itself as the most important bus assembler in Mexico, it has had important challenges such as the renewal of its products and the introduction of new technologies in the Mexican market.
OBJECTIVES
- Going beyond “Lean Tools” to align the entire organization both vertically and horizontally to set up the framework for daily management system to engage every level of management and team members towards driving business results
- Hands on development of selection of Hoshin “Breakthrough Focus Items”
- Learn by Doing, Creating, Implementing and Measuring key performance metrics and targets in the areas of Safety, Quality, Delivery and Cost (SQDC) as well as the standard work which evaluates each along with audit strategies
- Identifying and Coaching Improvement (small steps) and Innovation (large leaps) focused on Value to the Customer
- Learning what Plan-Do-Check-Adjust looks like at each management level and what processes are required to support it
- Setting the “framework” for:
- Lean Leadership System
- Lean Management System
- Lean Development System
- Lean Work System
- Take “working knowledge” and an action plan back to their home organization in order to take the appropriate next steps in their own lean transformation
AIMED AT:
- Top Management: CEO, COO, CFO, VPO,
- General Management.
- Plant manager.
- General Managers.
- Management.
PROGRAM
GALLERY OF PREVIOUS COURSES
INSTRUCTOR
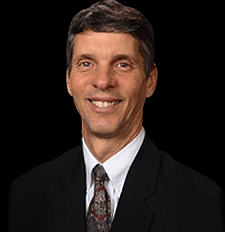
MICHAEL HOSEUS
ALFRA Toyota Team Director Former Executive Plant Manager of Toyota Kentucky
- Best Seller of the Toyota Culture
- Associate Executive Advisor for ALFRA Lean Advisors
- Former Toyota Assistant General Manager
- Former Assistant General Manager and Human Resources
- Executive Director CQPO
Mike is Executive Director for the Center for Quality People & Organizations (CQPO). Mike Hoseus brings both manufacturing operations and specialization in Human Resource experience to CQPO. CQPO is an organization developed in 1999 as a vision of Toyota Motor Manufacturing to share Lean Quality philosophy and human resource practices with education, business, and community organizations. CQPO current projects with Toyota include New Hire selection and training process, Team Leader and Group Leader post promotion training, Quality Circle Leader and Manager training, and Global Problem Solving for all levels. Mike is an adjunct professor with the University of Kentucky’s Lean Manufacturing Program. Mike is co author with Dr. Jeffery Liker (Author of the Toyota Way) of Toyota Culture. Mike is an adjunct professor with the University of Kentucky’s Center for Manufacturing and a member of the faculty of Lean Enterprise Institute. Mike is also president of Lean Culture Enterprises. Prior to CQPO, Mike was a corporate leader for 13 years at Toyota Motor Manufacturing’s Georgetown, Kentucky, plant both in Human Resources and Manufacturing. As Assistant General Manager in Human Resources, his responsibilities included personnel, safety, HR development, employee relations, benefits, training, and manufacturing/human resource teams for a plant of 8000 team members. His major initiative was development of the enhanced relationship between Human Resource and Manufacturing Mike’s operational responsibilities in manufacturing started in 1987 as a front line supervisor in vehicle assembly. This included all aspects of safety, quality, productivity, cost and morale for operations. With experience as Assembly Plant Manager and eventually Assistant General Manager, his responsibilities increased to include both assembly plants including operations, maintenance, and engineering. He is a Certified Trainer in Global Problem Solving & Waste Reduction, Standardized Work and Kaizen Events.
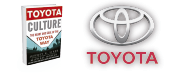
SERVICES INCLUIDED
- Manual
- Coffee break & Lunch
- Course Certificate.
- Simultaneous Translation Service ($130.00 MN + Tax / per day)