DESCRIPCIÓN
Entender los conceptos de Lean aplicados en Cadena de Suministros para operar la misma como un sistema dinámico y efectivo.
Contar con un panorama de la aplicación de los principios Lean en distintos escenarios para reducir inventarios de MP, WIP, PT.
Realizar un análisis de los procesos logístico y productivo que permita identificar áreas de oportunidad alrededor de los inventarios.
BENEFICIOS
- Manejo y Reducción de inventario en Almacenes
- Administración y Reducción del WIP
- Administración y Reducción de Producto Terminado
- Aumento del % de Entregas a tiempo
- Certeza de inventarios
- Certeza de compromisos a Cliente
OBJETIVOS
-
El Programa se divide en 3 partes:
– La primera parte cubren los conceptos generales de Lean aplicada en Cadenas de Suministro, los Mapas de Cadena de Suministro para identificar áreas de oportunidad a nivel sistémico y aplicaciones prácticas de los procesos de los participantes.
– La segunda parte consta de la revision de los enfoques y herramientas de Lean con Proveeduría, Planta y Producto Terminado que permiten preveer y reducir el inventario.
– La última parte consta de la identificación de Oportunidades de los procesos de los participantes, generando el Diseño del Mapa Futuro y aterrizando en un Plan de Acción Estratégico Lean para el logro de la Reducción de Inventarios de su Empresa.
DIRIGIDO A
Directores e Ingenieros de Materiales, Logística, Cadenas de Suministro, Planeación, Compras, Almacenes, Producción, Manufactura, Mejora Continua
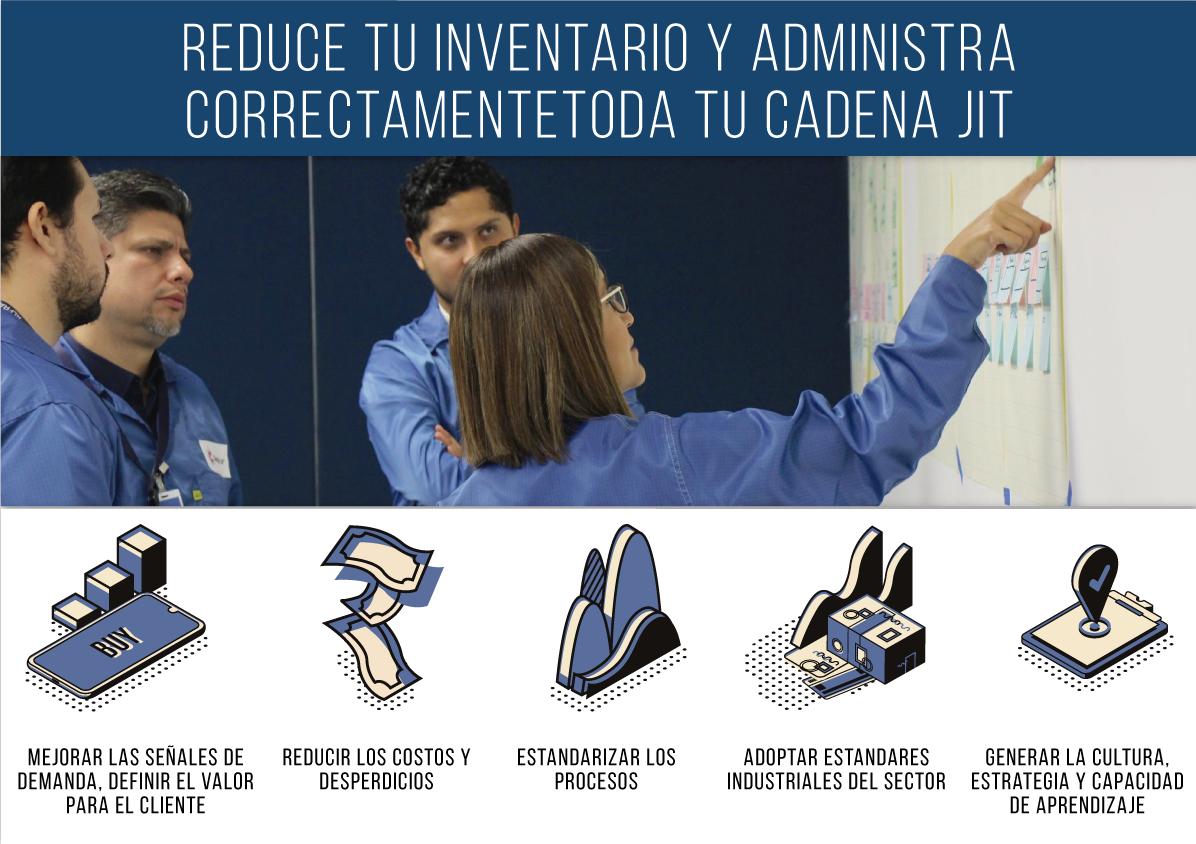
AGENDA
Semana 1 | Semana 2 |
---|---|
Día 1 Martes Jun 15 7:00pm 9:00pm Module II: Día 2 Jueves Jun 17 7:00pm 9:00pm Module IV:
|
Día 1 Martes Jun 22 7:00 pm 9:00pm Module VI: |
EXPOSITOR
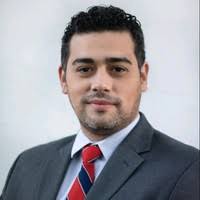
RODOLFO BOJORQUEZ
Professional Summary
- Karcher Mexico Materials Manager
- Amphenol Cemmex Logistics Manager
- JCI Components Plant Planning and Production Controls Manager
Rodolfo is an Advisor for Lean Operations with experience in global companies within Strategic Planning, Lean Operations, Supply Chain, HR, Sales & Finance.
He has been learning and developed on improve the all Supply Chain in Industrial environment. Using tools of Toyota Production System and Six Sigma Rodolfo has impacted positively the Supply reducing lead times, Inventories, improving processes, etc. Creating more lean operations and supporting people.
As expatriate on USA for JCI, he was able to support implementation of ERP SAP to improve process and quality of supply chain on 3 plants.
Rodolfo is a change agent enrolled with the high demand of the automotive industry, focused on results, but not leaving human side, values and caring for business interests
For over 15 years he has been constantly trained and deploying Improvement Projects to maximize as much resources possible to make thing better and easier, Rodolfo has been trained in the Toyota Way Culture, connecting the Lean Supply for the customers.
Rodolfo can help your team to accomplish their goals, to make things happen, meaning Business Transformation on Lean Supply to Lean Culture

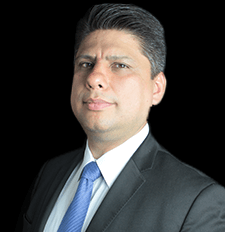
GUSTAVO VARELA
Former American Standard Continuous Improvement Director
Former Daltile Master Black Belt
22 years experience. +17 years as Global Continuous Improvement Leader
Based on his broad experience, Gustavo is expert applying a suitable approach for Continuous Improvement needed on the different organizations from a Business results optic, becoming an effective Coach for Top Management and support for The Toyota Way roles.
Gustavo has learned The Toyota Way directly from its Author, Dr. Jeff Liker, and has applied it on Gemba as a Team with many Executives from Toyota specialized on General Management, TPM, Lean Mfg Tools, and Supply Chain. Gustavo has taught the Toyota Production System at all organizational levels and has applied over 50 companies of different sizes: Lean Leadership Systems (Hoshin Kanri, FMDS, and 8-Step Problem Solving), Toyota Kata for development, Supply Chain Management, TPM, Lean Manufacturing tools (5S’s, SW, SMED, Jidoka, Poka Yoke, Heijunka, JIT, etc.), and Lean Officeapproach. On Six Sigma, Gustavo as Master Black Belt has trained and certified +500 Black Belts, Green Belts, and Yellow Belts.
Gustavo has +20 years of experience on Continuous Improvement, Manufacturing, Process Engineering and Quality in large companies: Motor Wheel (Automotive), Kodak, Philips, Daltile, American Standard. He has +12 years of experience as Vice/President Staff as Continuous Improvement Director for American Standard México and Master Black Belt Champion for Daltile México. He has deployed programs that have achieved +$110 Million USD in savings with +3,000 projects on all departments: R&D, Engineering, Manufacturing, Maintenance, Quality, Logistics, Supply Chain, Sales, Marketing, Finance, HR, Energy. Over his 22 years experience, Gustavo has been exposed to many different organizations applying suitable Lean approaches on a variety of systems with diversity on leadership styles.

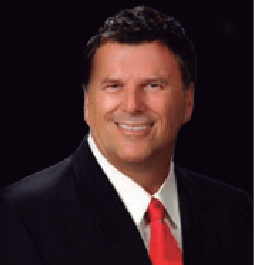
JEFF MERRIS
Mechanical Engineering with Mayor on Business Management. Former Toyota TABC Manager. Former ToyotaAssistant Manager of Production Control. +25 years Toyota Experience at Toyota.
+25 YEARS TOYOTA EXPERIENCE Education · Mechanical Engineering with Mayor on Business Management. Jeff Merris have worked for Toyota Motor Manufacturing for 24 years and as an independent consultant for the past 2 years. During my career I have implemented TPS (lean production) in the Automotive (Toyota), snack food, beverage and the airline industries. Primary focus has been improvement in Production Planning, Internal Logistics (conveyance), External Logistics, Manufacturing and Finance. He has experience on create 1, 3, 5 year business plan, develop Strategies to integrate current business models with new business, develop and implement internal and external logistics strategies, develop and implement cross – dock (warehouse) strategies, develop and Implement Short and Long Term Production Plans to meet customer needs, develop production plan to meet TAKT time, teach & coach Toyota Problem Solving, develop and Implement Kanban Systems(material replenishment), develop manufacturing support equipment and develop internal delivery dollies. Merris has a Mayor on Mechanical Engineering by University of Kentucky (1983-1987), Major on Business Management by Northwood University (2005-2007). He was Production Control Assistant Manager from 2005 to 2007, Assistant Manager Production Control from 1997 to 2003, and Team Leader, Production Engineer (1988-2003) – at Toyota Motor Manufacturing Kentucky.