WORKPLACE ORGANIZATION
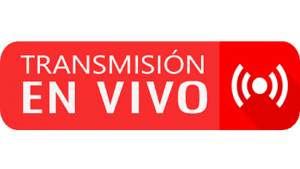
WHY IS THIS PILLAR IMPORTANT?
This is an interactive pillar that has the responsibility to increase productivity and is supported by some pillars such as Safety, Logistics, Quality, Autonomous maintenance, Focus improvement, Cost deployment and People development.
This pillar participates with People development to provide good training to the operators or team members and help them to eliminate the following things: Walking, waiting, excess of material, human errors, scrap, hard to place, hard to reach, etc.
Motivation, engagement and accountability of employees is key to assure every team score card and the end the Plant score card.
VISION
Plant employees must be empowered to develop a workplace in which safety, production process activities and quality are benchmark in the industry and well supported by excellent standards bring as a result the lowest manufacturing cost.
OBJECTIVES
- Remove roadblocks in order to attain higher levels of quality and productivity.
- Operators continuously improve the ability to identify and eliminate losses.
- All team member activities improves with rigor, pace and participation increasing knowledge.
- Human Errors are eliminating with all pillar participation.
AGENDA
1.- Identification of losses in the production process.
2.- Initial cleaning
3.- Reorganize the production process eliminating Muri, Mura and Muda and ensure the correct balancing of the lines, increasing productivity
4.- Initial production standards
5.- Understand the classification of operators and their involvement in quality systems.
6.- correct use of the tools read in each of the steps.
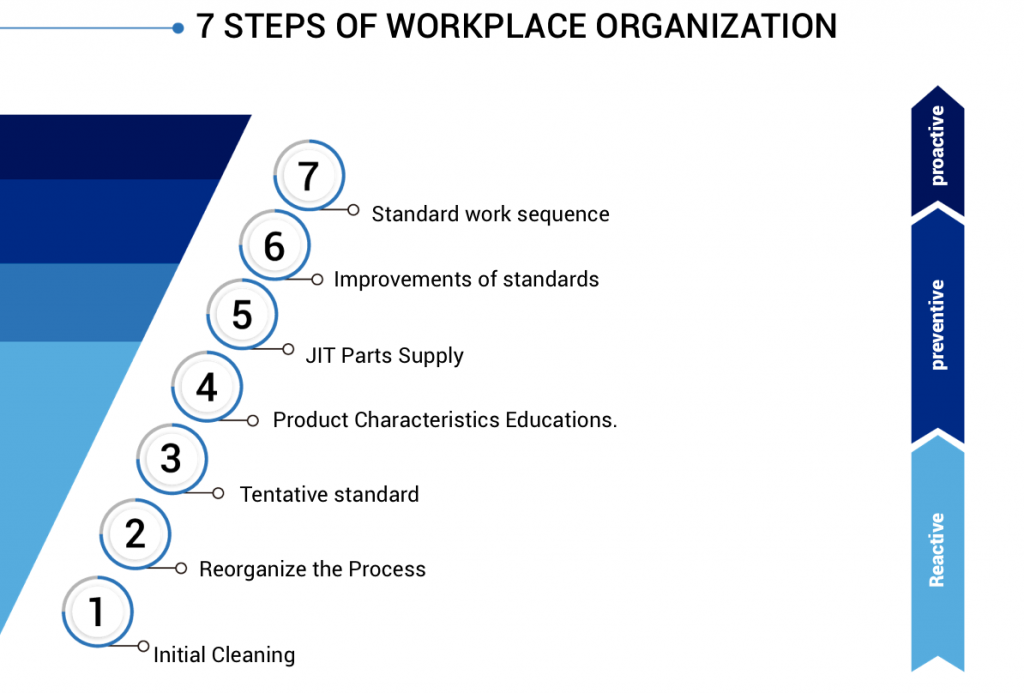
Lean Leaders Congress
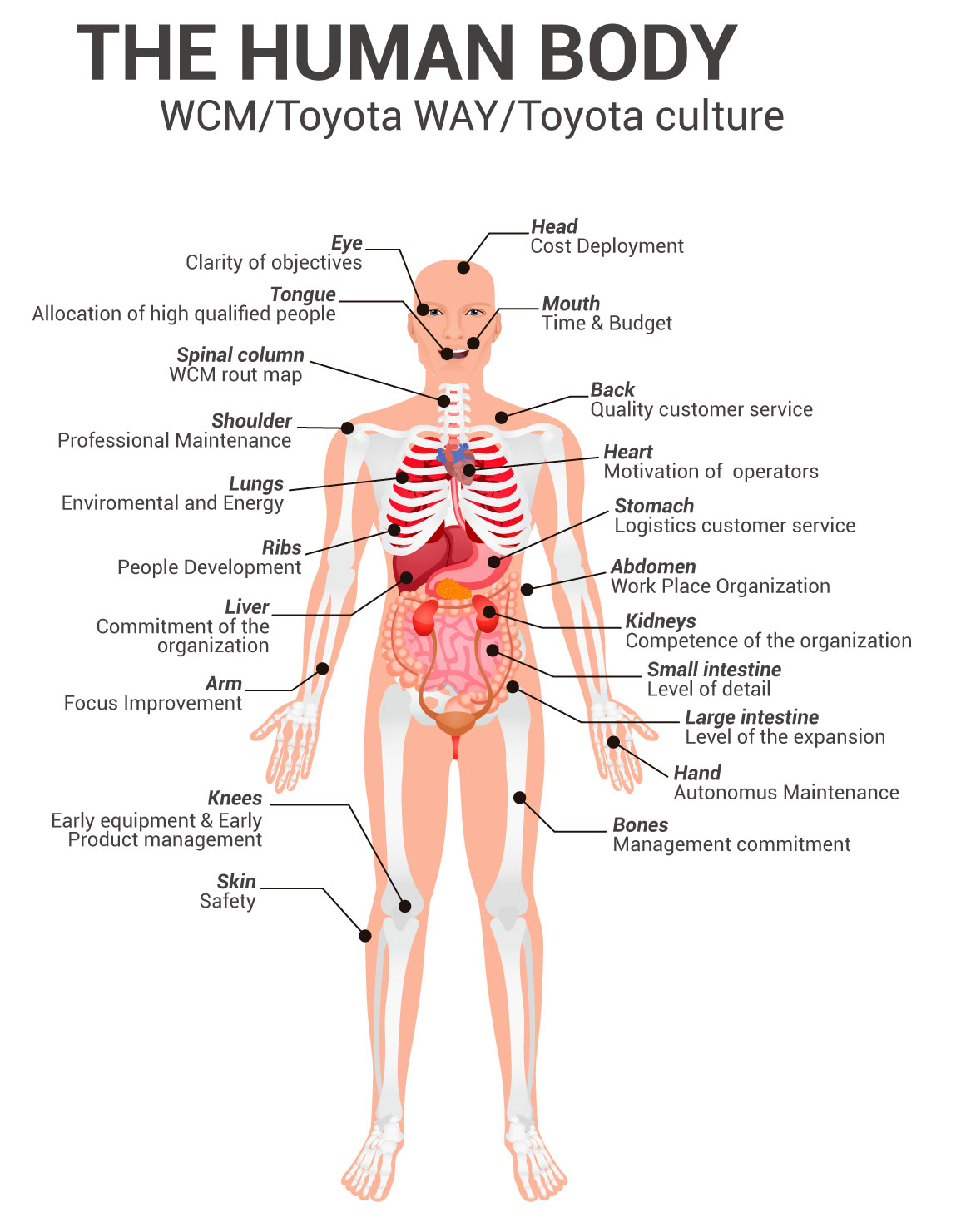
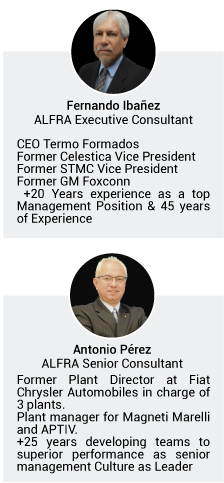
WCM TEAM
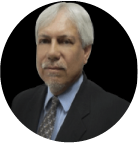
Fernando Ibañez
ALFRA Senior Advisor
CEO Termo Formados
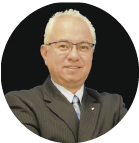
Antonio Pérez
ALFRA Senior Consultant Director
Former Plant Director
at Fiat Chrysler Automobiles
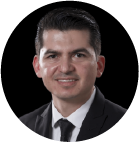
Francisco Ocejo
ALFRA Global Director & Founder
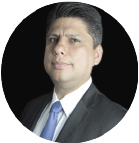
Gustavo Varela
ALFRA Consulting Division Director
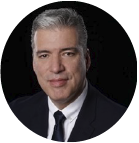
Eduardo Varela
ALFRA Executive Advisor
Former Multi-site Regional Director
for Mexico at Berry Global
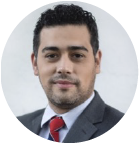
Rodolfo Bojorquez
ALFRA Lean Consultant
Former Karcher Mexico Materials Manager
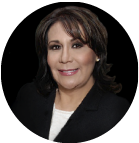
Olivia Gallardo
KATA Organizational Excellence (KOX)
Focus on Lean Culture Owner & Founder
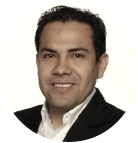
Javier Hernandez
ALFRA Senior Lean Advisor
Former Lean Manager and
New Product Introduction Leader at mabe
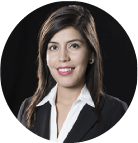
Lidia Flores
ALFRA Lean Consultant Specialist
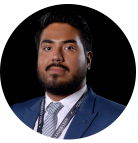
Edgar Cárdenas
ALFRA Europe Operations Director
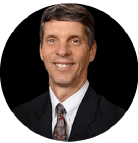
EVALUATOR
Michael Hoseus
Best Seller of the Toyota Culture
Former Toyota Assistant General Manager
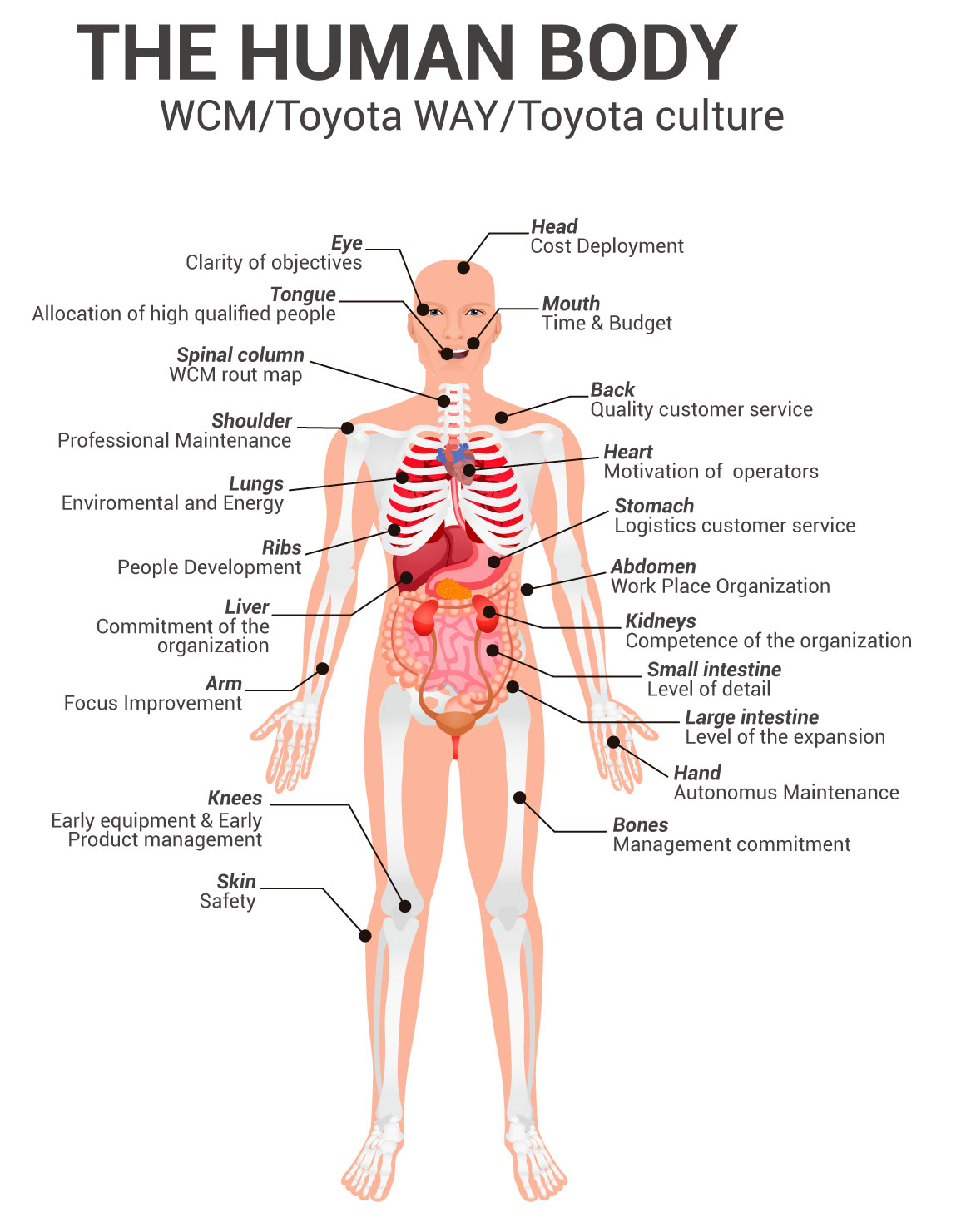
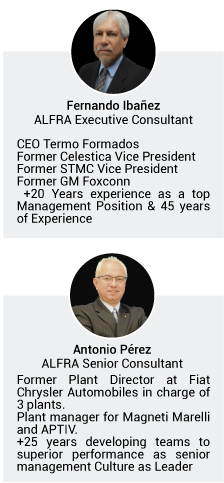